Custom Plastic Extrusion vs. Injection Molding: Which is Right for Your Project?
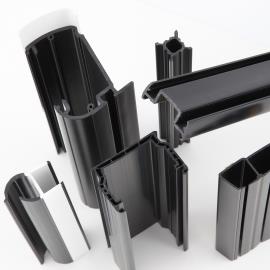
Custom Plastic Extrusion vs. Injection Molding: Which is Right for Your Project?
When it comes to manufacturing plastic products, two of the most common processes are custom plastic extrusion and injection molding. Both processes have their pros and cons, and choosing the right one for your project can make a big difference in the final product`s quality, cost, and speed of production. In this article, we`ll explore the differences between custom plastic extrusion and injection molding, as well as the advantages and disadvantages of each process. By the end of this article, you`ll have a better understanding of which process is right for your specific project.
Differences between Custom Plastic Extrusion and Injection Molding
Custom plastic extrusion is a manufacturing process where plastic material is melted and formed into a continuous profile, such as tubing, pipe, or a custom shape. The plastic material is fed through a machine, where it is heated and then pushed through a die that gives it its final shape. The finished product can be cut to the desired length and shipped to the customer. Injection molding, on the other hand, involves melting plastic pellets and injecting them into a mold to create a finished product.Product Types and Materials
One of the main differences between custom plastic extrusion and injection molding is the types of products that can be made using each process. Custom plastic extrusion is better suited for creating continuous profiles or custom shapes that are long and narrow, like tubing or pipe. Injection molding, on the other hand, is better suited for creating more complex shapes with multiple features, such as gears, buttons, and other parts with varying thicknesses. Another difference between the two processes is the materials used. Custom plastic extrusion can use a wide variety of materials, including PVC, HDPE, nylon, and polycarbonate, among others. Injection molding can also use these materials, but it is typically better suited for materials that require high precision, like ABS, polystyrene, and polypropylene.When to Use Custom Plastic Extrusion
Custom plastic extrusion is best suited for projects that require continuous profiles or long, narrow shapes. This process is also a good choice for creating custom shapes with simple features, such as a U-shaped channel or a square tube. Custom plastic extrusion is also a good choice when the project has a low volume or requires a quick turnaround.Advantages of Custom Plastic Extrusion
Custom plastic extrusion has several advantages over injection molding. First, it is a more cost-effective option for low-volume production runs. Second, it offers a quick turnaround, allowing you to get your product to market faster. Third, it offers a wide variety of materials, including those that are difficult to mold using injection molding. When to Use Injection Molding Injection molding is better suited for projects that require complex shapes with varying thicknesses, multiple features, and tight tolerances. It is also a good choice for projects that require a large volume of parts, as the cost per part decreases as the volume increases. Injection molding is also a good choice when the product needs to be consistent in size and shape. Advantages of Injection Molding Injection molding has several advantages over custom plastic extrusion. First, it offers higher precision, allowing for more complex shapes and tighter tolerances. Second, it has a lower cost per part for larger production runs. Third, it can produce parts with multiple features and varying thicknesses in one shot, which can reduce assembly time and cost. Pros and Cons of Custom Plastic Extrusion vs. Injection Molding Each process has its advantages and disadvantages, and choosing the right process for your project depends on several factors. Here is a quick summary of the pros and cons of custom plastic extrusion and injection molding:Custom Plastic Extrusion:
- Pros: Lower upfront cost, quick turnaround, good for low-volume runs, wide variety of materials
- Cons: Limited to simple shapes, less precise than injection molding, not suited for high-volume runs
Injection Molding:
- Pros: Higher precision, better for complex shapes, lower cost per part for large runs, can produce parts with multiple features and varying thicknesses
- Cons: Higher upfront cost, longer lead times for molds, not suited for low-volume runs
Conclusion
In conclusion, choosing between custom plastic extrusion and injection molding depends on several factors, including the complexity of your product, the volume of production, the materials you are using, and your budget. Both processes have their pros and cons, and understanding the differences between them can help you make the right choice for your project. If you need help deciding which process is right for your project, reach out to a reputable plastic manufacturer who can help guide you through the process.
Latest News
-
20 Ridgeway Road, Edinburgh North 5113 South Australia
Contact Us
Address: 20 Ridgeway Road, Edinburgh North 5113 South Australia
Email: sales@pacerprofiles.com.au