The Future is Extruded: Innovative Applications of Plastic Extrusion Products
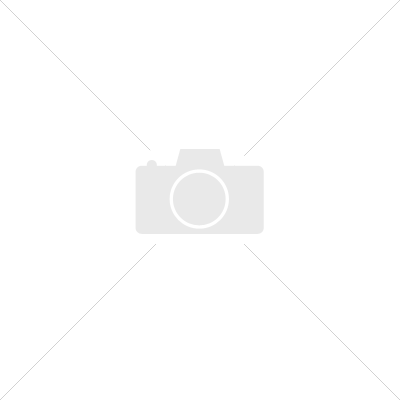
The Future is Extruded: Innovative Applications of Plastic Extrusion Products
Plastic extrusion products have become a driving force in various industries, providing versatile solutions for a wide range of applications. These products are created through the process of plastic extrusion, where molten plastic is forced through a die to produce continuous profiles of different shapes and sizes. While plastic extrusion has been used for decades, it is the innovative applications that are shaping the future of this technology. In this blog post, we will explore some of the groundbreaking applications of plastic extrusion products and their impact on industries ranging from automotive to healthcare.
I. Automotive Industry
The automotive industry has embraced plastic extrusion products for their ability to revolutionize vehicle design and manufacturing. Extruded plastic components offer light weighting solutions, contributing to improved fuel efficiency and reduced emissions. From extruded plastic profiles for bumper systems to weatherstrips and interior trim, plastic extrusion is playing a crucial role in enhancing both the aesthetics and functionality of automobiles. Furthermore, the flexibility of plastic extrusion allows for the production of complex shapes and geometries, enabling innovative design possibilities.II. Building and Construction
Plastic extrusion products are making a significant impact in the building and construction sector, providing durable and cost-effective solutions. Extruded plastic profiles are used for windows, doors, and roofing systems, offering superior insulation properties and resistance to weather conditions. These profiles can be customized to fit specific architectural requirements, providing design flexibility for architects and builders. Plastic extrusion products also contribute to energy efficiency, as they minimize heat transfer and reduce the overall carbon footprint of buildings.III. Packaging Industry
In the packaging industry, plastic extrusion products are transforming the way products are packaged, stored, and transported. Extruded plastic films and sheets are used for flexible packaging solutions, offering advantages such as lightweight, flexibility, and barrier properties. These films can be engineered to provide specific barrier functions like oxygen and moisture resistance, extending the shelf life of perishable products. Furthermore, plastic extrusion enables the production of customized packaging designs, enhancing brand recognition and consumer appeal. The use of extruded plastic packaging also contributes to sustainability efforts, as it can be recycled and reused.IV. Medical and Healthcare
Plastic extrusion products have become indispensable in the medical and healthcare field, where precision and safety are paramount. Extruded plastic tubes, catheters, and medical devices offer sterile and biocompatible solutions for various medical procedures. The versatility of plastic extrusion allows for the production of intricate and small-diameter tubes, enabling minimally invasive procedures. These extruded medical components are also disposable, reducing the risk of contamination and infection transmission. Plastic extrusion has played a significant role in advancing medical technology, improving patient outcomes, and driving innovation in the healthcare industry.V. Environmental Sustainability
In addition to their various applications, plastic extrusion products are contributing to environmental sustainability. The use of extruded plastic profiles in renewable energy systems, such as solar panels and wind turbines, is on the rise. These profiles provide structural support, durability, and resistance to environmental factors, making them ideal for renewable energy applications. Plastic extrusion also plays a crucial role in the development of eco-friendly packaging solutions. By utilizing recycled plastics and optimizing material usage, extruded plastic packaging reduces waste and supports circular economy principles.VI. Advancements in Material Science
One of the key drivers behind the innovative applications of plastic extrusion products is the continuous advancements in material science. Researchers and engineers are constantly exploring new materials and developing specialized polymers specifically tailored for the extrusion process. These materials offer enhanced properties, such as increased strength, heat resistance, and chemical resistance, opening up new possibilities for applications in various industries.For example, high-performance polymers, such as polyethylene terephthalate (PET), polyetheretherketone (PEEK), and polycarbonate (PC), have gained popularity in the automotive and aerospace sectors. These materials possess excellent mechanical properties, allowing for the production of lightweight and durable components. Additionally, they exhibit superior resistance to extreme temperatures, making them suitable for demanding environments.VII. Conclusion
Plastic extrusion products have come a long way since their inception, and their future looks promising. The innovative applications of plastic extrusion are transforming industries such as automotive, building and construction, packaging, and healthcare. From lightweight automotive components to energy-efficient building materials, plastic extrusion products are revolutionizing the way we design, manufacture, and use products. Moreover, their contribution to environmental sustainability is significant, with extruded plastic profiles supporting renewable energy systems and eco-friendly packaging solutions.Latest News
-
20 Ridgeway Road, Edinburgh North 5113 South Australia
Contact Us
Address: 20 Ridgeway Road, Edinburgh North 5113 South Australia
Email: sales@pacerprofiles.com.au