Custom Plastic Extrusion: Enhancing Product Performance and Efficiency
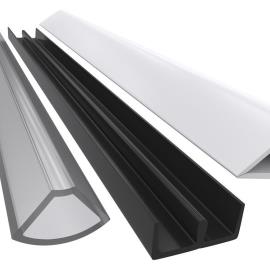
Custom Plastic Extrusion: Enhancing Product Performance and Efficiency
Plastic extrusion products are used in a variety of industries for different purposes. They are created through the process of plastic extrusion, which involves melting plastic materials and forcing them through a die to form a continuous profile or shape. Custom plastic extrusion allows for the creation of specific shapes and sizes of plastic extrusion products to meet the needs of specific applications. This blog will provide an overview of plastic extrusion products and their benefits, as well as highlight the importance of custom plastic extrusion.Types of Plastic Extrusion Products
There are several types of plastic extrusion products, including tubes and pipes, profiles and shapes, and films and sheets. Each type has unique properties that make it suitable for specific applications.Tubes and PipesPlastic tubes and pipes are commonly used in the construction and automotive industries, as well as for medical devices. They are lightweight and can be easily molded into different shapes and sizes, making them ideal for a variety of applications.Profiles and ShapesPlastic profiles and shapes are used in a variety of industries, including construction, automotive, and consumer goods. They can be customized to meet the specific needs of each application, making them an ideal choice for manufacturers.Benefits of Plastic Extrusion Products
There are several benefits to using plastic extrusion products, including their durability and strength, cost-effectiveness, versatility, and resistance to environmental factors.Durability and StrengthPlastic extrusion products are known for their durability and strength, making them ideal for use in applications that require a high level of durability, such as construction and automotive.Cost-effectivenessPlastic extrusion products are often more cost-effective than other materials, such as metal or wood. They are lightweight, which reduces shipping costs, and can be easily molded into different shapes and sizes, reducing the need for additional processing or manufacturing.VersatilityPlastic extrusion products are versatile and can be customized to meet the specific needs of each application. They can be molded into a wide range of shapes and sizes, and can be made from a variety of materials, making them an ideal choice for manufacturers.Resistance to Environmental FactorsPlastic extrusion products are resistant to environmental factors such as moisture, chemicals, and UV light. This makes them an ideal choice for outdoor applications, as well as for use in harsh environments.Importance of Custom Plastic Extrusion
Custom plastic extrusion allows for the creation of specific shapes and sizes of plastic extrusion products to meet the needs of specific applications. This is important for several reasons, including meeting unique specifications, enhancing product functionality, and increasing production efficiency.Meeting Unique SpecificationsCustom plastic extrusion allows manufacturers to create products that meet unique specifications, such as specific dimensions or shapes. This is important in industries such as construction and automotive, where each application has unique requirements.Enhancing Product FunctionalityCustom plastic extrusion allows manufacturers to enhance the functionality of their products. By creating specific shapes and sizes, manufacturers can improve the performance of their products, resulting in increased customer satisfaction and improved sales.Increasing Production EfficiencyCustom plastic extrusion can also help manufacturers increase production efficiency. By creating products that are tailored to specific applications, manufacturers can reduce waste and streamline their production processes. This can result in cost savings and increased profitability.Applications of Plastic Extrusion Products
Plastic extrusion products are used in a variety of industries for different applications. Some of the most common applications include construction and building, automotive, and medical devices and equipment.Construction and Building
Plastic extrusion products are commonly used in the construction and building industry for applications such as window and door frames, roofing materials, and siding. Plastic extrusion products are durable, lightweight, and cost-effective, making them an ideal choice for these applications.Automotive
Plastic extrusion products are also used in the automotive industry for applications such as interior and exterior trim, fuel and brake lines, and air intake systems. Plastic extrusion products are lightweight and durable, which can improve the fuel efficiency and performance of vehicles.Medical Devices and Equipment
Plastic extrusion products are used in the medical industry for applications such as tubing and catheters. Plastic extrusion products are biocompatible and can be easily sterilized, making them an ideal choice for medical applications.
Conclusion
Plastic extrusion products are used in a variety of industries for different applications. Custom plastic extrusion allows manufacturers to create specific shapes and sizes of plastic extrusion products to meet the needs of specific applications. Plastic extrusion products offer several benefits, including their durability and strength, cost-effectiveness, versatility, and resistance to environmental factors. They are commonly used in the construction and building, automotive, and medical industries. The importance of custom plastic extrusion cannot be overstated, as it allows manufacturers to meet unique specifications, enhance product functionality, and increase production efficiency.
Latest News
-
20 Ridgeway Road, Edinburgh North 5113 South Australia
Contact Us
Address: 20 Ridgeway Road, Edinburgh North 5113 South Australia
Email: sales@pacerprofiles.com.au